
When you ask for assistance it is always best to attach the Fusion file to your Post, in Fusion go to "File > Export and save out as an f3d format file to a location on your PC and then put it in a Zip folder and using the "Advanced" option on your reply upload the Zip file, unless it is a "proprietry" customer design that you don`t want anyone to see in which case you can email it to someone on here for their assistance. When you create the objects either from Primitive solids or from Sketches you will automatically be starting from a selected Plane and you should always extrude the height in a negative direction (Downwards), that way all the tops of the objects will be at the same height and you will just be cutting different depths in your stock sheet to suit the different thickness of each object. ThanksAre you saying that your objects are different thicknesses?ĭid you create them by extruding upwards in the "Design" mode and you now have a lot of different Top heights?
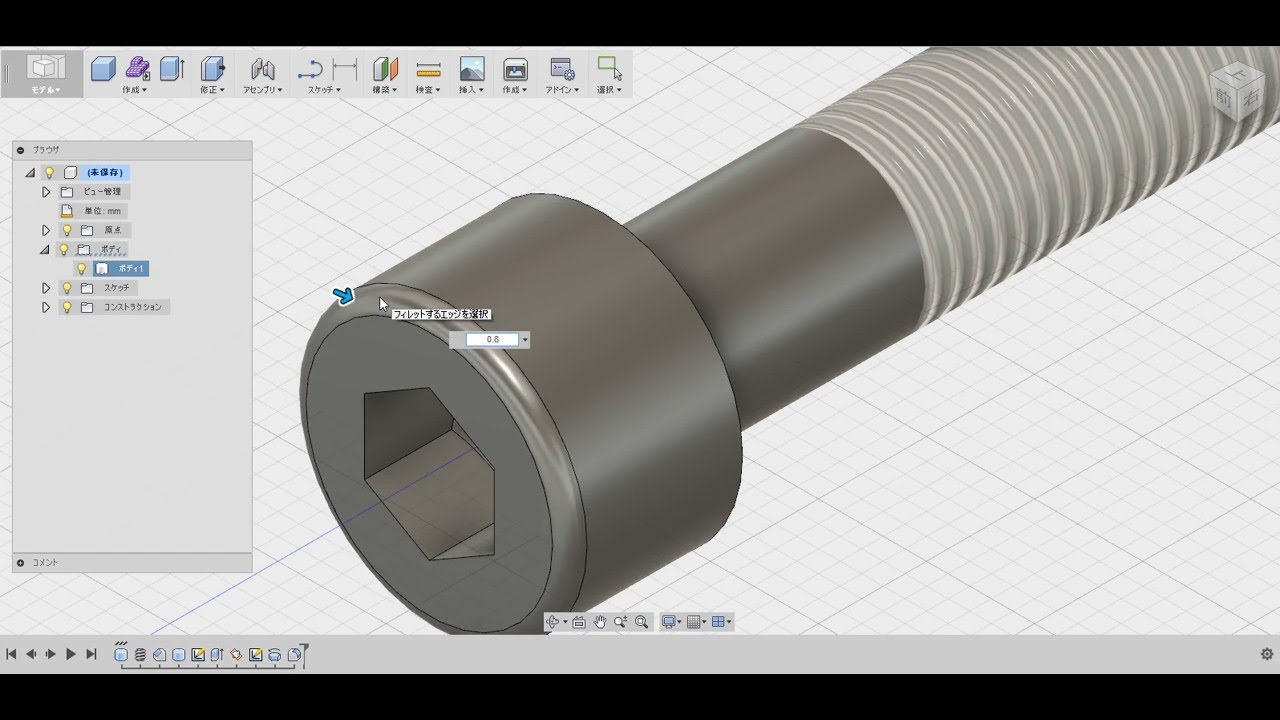
They are inlays I want to cut out on a single piece of wood, I hope I used the right terminology there.Īlso I understand I need to round the corners off on both my inlay and my recesses the inlays sit in to match the tool is there any guides on how to do this correctly or is it trial and error? I have 13 objects that have different Z axis heights in my fusion model now for manufacture I want to put all 13 on the same Z axis plane.
